The Importance of Auxiliary Equipment in Blow Molding
By:Admin
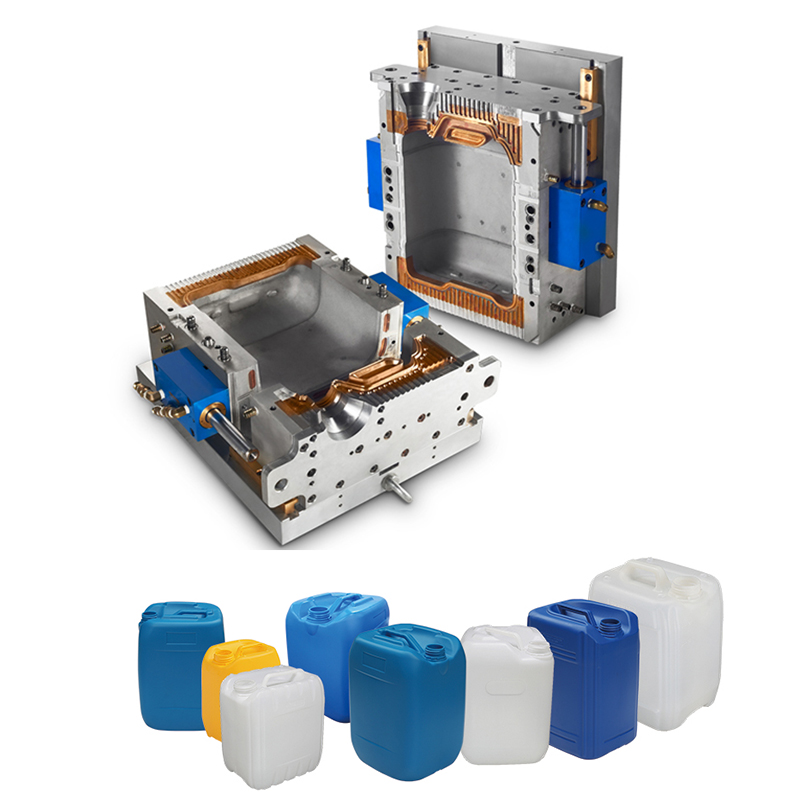
Introduction:
Blow molding is a widely used manufacturing process in the production of plastic containers and bottles. To ensure the efficiency and quality of the blow molding process, the utilization of various auxiliary equipment is of paramount importance. These tools aid in enhancing productivity, maintaining consistent output, and ensuring the overall success of the blow molding operation. In this article, we will explore the significance of auxiliary equipment in the blow molding industry, encompassing its role, types, and benefits.
Role of Auxiliary Equipment:
Auxiliary equipment plays a pivotal role in supporting and enhancing the efficiency of the blow molding process. These devices are designed to assist in different stages of the manufacturing cycle, such as material handling, controlling temperature, cutting, trimming, and a myriad of other operations. By integrating auxiliary equipment, manufacturers can streamline their production lines, reduce manual labor, enhance product quality, and achieve higher levels of output.
Types of Auxiliary Equipment in Blow Molding:
1. Material Handling Equipment:
- Conveyors: These devices assist in moving raw materials, preforms, and finished products through each stage of the blow molding process, ensuring smooth material flow and minimizing human intervention.
- Hoppers: Hoppers aid in the organized storage and feeding of plastic resins or pellets into the extruder. They help regulate the supply of raw materials, preventing interruptions and ensuring an uninterrupted production line.
2. Temperature Control Equipment:
- Chillers: These devices are crucial for maintaining consistent cooling temperatures during the blow molding process. Chillers control the temperature of molds, ensuring the final product's dimensional accuracy and quality.
- Mold Temperature Controllers: These controllers regulate the temperature of the molds themselves, preventing fluctuation and ensuring consistent heat distribution. By maintaining optimal mold temperatures, manufacturers can achieve faster production cycles and improve product quality.
3. Cutting and Trimming Equipment:
- Guillotine Cutters: These devices aid in cutting or trimming the excess material from the finished blow-molded items. They enable precise and accurate trimming, contributing to a polished final product.
- Deflashing Equipment: Deflashing machines are used to remove excess material or flash from the finished products. These machines improve the overall appearance and functionality of the final blow-molded items.
4. Quality Control Equipment:
- Inspection Systems: These systems employ advanced imaging technologies to detect and eliminate any defects or inconsistencies in the finished products. By incorporating inspection systems, manufacturers can maintain the desired quality levels and ensure consumer satisfaction.
Benefits of Incorporating Auxiliary Equipment:
1. Improved Efficiency: Auxiliary equipment streamlines the manufacturing process, reducing manual labor and improving overall efficiency. It decreases downtime and minimizes errors, resulting in higher productivity and increased profitability.
2. Enhanced Product Quality: By incorporating auxiliary equipment, manufacturers can achieve consistent product quality. Temperature control equipment, cutting and trimming devices, and inspection systems all contribute to delivering flawless products to the market.
3. Cost Reduction: The integration of auxiliary equipment reduces material wastage, improves energy efficiency, and minimizes the need for manual labor. These factors lead to significant cost savings for manufacturers in the long run.
4. Scalability: Auxiliary equipment is crucial for accommodating increased production volumes. By having the appropriate tools in place, manufacturers can easily scale their operations without compromising on quality or efficiency.
Conclusion:
Auxiliary equipment is indispensable in the blow molding industry, enabling manufacturers to achieve efficient and high-quality production processes. The integration of material handling equipment, temperature control devices, cutting and trimming tools, and quality control systems ensures smooth operations, consistent output, and reduced costs. By leveraging the benefits of auxiliary equipment, manufacturers can stay competitive in the ever-evolving market of blow molding.
Company News & Blog
Ultimate Guide to Choosing the Best Cosmetic Packaging for Your Products
Cosmetic Packaging: A Look at the Latest Trends and Innovations in Beauty PackagingIn recent years, the beauty industry has experienced a significant shift towards more sustainable and eco-friendly practices. This has extended to the packaging of cosmetic products, with brands and manufacturers increasingly seeking out sustainable and innovative packaging solutions. With this in mind, {Company Name} has been at the forefront of developing cutting-edge cosmetic packaging that not only meets the needs of their clients but also aligns with their commitment to sustainability.{Company Name} has a long-standing reputation for producing high-quality cosmetic packaging for some of the leading beauty brands in the industry. With a focus on innovation and sustainability, the company has been able to stay ahead of the curve in a rapidly evolving market. Their team of experts is constantly researching and designing new packaging solutions that not only meet the functional requirements of their clients but also reflect the latest trends and consumer preferences.One of the key trends in cosmetic packaging is the move towards more sustainable and eco-friendly materials. {Company Name} has been actively developing and promoting the use of materials such as recycled plastics, biodegradable plastics, and glass, all of which have a lower impact on the environment. In addition to using sustainable materials, the company also focuses on designing packaging with minimal environmental impact, such as reducing the use of unnecessary packaging and incorporating innovative designs that minimize waste.In line with the growing demand for sustainable packaging, {Company Name} has also been exploring new technologies and processes to further improve the environmental performance of their products. This includes investing in new manufacturing techniques that reduce energy consumption and waste, as well as exploring the potential of alternative materials and bioplastics. By integrating these sustainable practices into their operations, the company is not only meeting the demands of their clients but also contributing to the overall sustainability of the beauty industry.Another key trend in cosmetic packaging is the emphasis on functionality and user experience. {Company Name} recognizes the importance of creating packaging that not only looks aesthetically pleasing but also enhances the overall experience of using the product. This includes designing packaging with convenient dispensing systems, ergonomic shapes, and easy-to-use features that make the product more appealing to consumers.In addition to functionality, {Company Name} has also been incorporating innovative designs and packaging concepts that appeal to the modern consumer. This includes the use of bold colors, striking graphics, and unique shapes that stand out on the shelves and attract the attention of the target audience. By staying ahead of the curve in terms of design and aesthetics, the company is able to offer their clients packaging solutions that are both visually appealing and on-trend with the latest consumer preferences.As the beauty industry continues to evolve, {Company Name} remains committed to staying at the forefront of cosmetic packaging innovation. By focusing on sustainability, functionality, and design, the company is able to offer their clients cutting-edge packaging solutions that meet the demands of the modern consumer. With a strong emphasis on research and development, {Company Name} is well-positioned to continue driving innovation in the cosmetic packaging industry for years to come.
The Importance of Auxiliary Equipment in Blow Molding
Title: Essential Auxiliary Equipment in Blow Molding IndustryIntroduction:Blow molding is a widely used manufacturing process in the production of plastic containers and bottles. To ensure the efficiency and quality of the blow molding process, the utilization of various auxiliary equipment is of paramount importance. These tools aid in enhancing productivity, maintaining consistent output, and ensuring the overall success of the blow molding operation. In this article, we will explore the significance of auxiliary equipment in the blow molding industry, encompassing its role, types, and benefits.Role of Auxiliary Equipment:Auxiliary equipment plays a pivotal role in supporting and enhancing the efficiency of the blow molding process. These devices are designed to assist in different stages of the manufacturing cycle, such as material handling, controlling temperature, cutting, trimming, and a myriad of other operations. By integrating auxiliary equipment, manufacturers can streamline their production lines, reduce manual labor, enhance product quality, and achieve higher levels of output.Types of Auxiliary Equipment in Blow Molding:1. Material Handling Equipment: - Conveyors: These devices assist in moving raw materials, preforms, and finished products through each stage of the blow molding process, ensuring smooth material flow and minimizing human intervention. - Hoppers: Hoppers aid in the organized storage and feeding of plastic resins or pellets into the extruder. They help regulate the supply of raw materials, preventing interruptions and ensuring an uninterrupted production line.2. Temperature Control Equipment: - Chillers: These devices are crucial for maintaining consistent cooling temperatures during the blow molding process. Chillers control the temperature of molds, ensuring the final product's dimensional accuracy and quality. - Mold Temperature Controllers: These controllers regulate the temperature of the molds themselves, preventing fluctuation and ensuring consistent heat distribution. By maintaining optimal mold temperatures, manufacturers can achieve faster production cycles and improve product quality.3. Cutting and Trimming Equipment: - Guillotine Cutters: These devices aid in cutting or trimming the excess material from the finished blow-molded items. They enable precise and accurate trimming, contributing to a polished final product. - Deflashing Equipment: Deflashing machines are used to remove excess material or flash from the finished products. These machines improve the overall appearance and functionality of the final blow-molded items.4. Quality Control Equipment: - Inspection Systems: These systems employ advanced imaging technologies to detect and eliminate any defects or inconsistencies in the finished products. By incorporating inspection systems, manufacturers can maintain the desired quality levels and ensure consumer satisfaction.Benefits of Incorporating Auxiliary Equipment:1. Improved Efficiency: Auxiliary equipment streamlines the manufacturing process, reducing manual labor and improving overall efficiency. It decreases downtime and minimizes errors, resulting in higher productivity and increased profitability.2. Enhanced Product Quality: By incorporating auxiliary equipment, manufacturers can achieve consistent product quality. Temperature control equipment, cutting and trimming devices, and inspection systems all contribute to delivering flawless products to the market.3. Cost Reduction: The integration of auxiliary equipment reduces material wastage, improves energy efficiency, and minimizes the need for manual labor. These factors lead to significant cost savings for manufacturers in the long run.4. Scalability: Auxiliary equipment is crucial for accommodating increased production volumes. By having the appropriate tools in place, manufacturers can easily scale their operations without compromising on quality or efficiency.Conclusion:Auxiliary equipment is indispensable in the blow molding industry, enabling manufacturers to achieve efficient and high-quality production processes. The integration of material handling equipment, temperature control devices, cutting and trimming tools, and quality control systems ensures smooth operations, consistent output, and reduced costs. By leveraging the benefits of auxiliary equipment, manufacturers can stay competitive in the ever-evolving market of blow molding.
Blow Molding Machines: An In-Depth Look at Pricing and Factors to Consider
Blow Molding Machine Price: Driving Innovation and Affordability in the Manufacturing IndustryThe blow molding industry has experienced significant growth in recent years, fueled by increasing demand for plastic packaging and a rise in consumer preferences for affordable and lightweight materials. As a result, companies are constantly seeking innovative solutions to improve production efficiency and lower costs.One prominent player in this field, a global leader in blow molding machinery, has recently unveiled a new line of blow molding machines that promise to revolutionize the manufacturing industry. With a focus on affordability without compromising quality, the company aims to equip manufacturing businesses with highly efficient tools that meet their production needs at a competitive price point.Blow molding machines are essentially used to create hollow plastic parts and containers in a wide range of industries, including food and beverage, cosmetics, pharmaceuticals, and automotive. These machines employ a process of melting plastic resins and stretching them into a desired shape, resulting in strong and lightweight products.The newly introduced blow molding machines by this industry-leading company incorporate advanced technology and numerous features designed to enhance productivity and reduce downtime. These machines offer improved automation, precision controls, and faster cycle times, ensuring more efficient production rates. By streamlining the manufacturing process, businesses can achieve higher output and lower costs, ultimately resulting in a competitive edge.One of the standout features of this new line of blow molding machines is their versatility. With the ability to produce a wide variety of shapes and sizes, these machines cater to the diverse needs of manufacturers. Whether it's producing bottles, containers, or other bespoke plastic products, the flexibility of these machines allows businesses to adapt to changing market demands without significant retooling or investment.In addition to their technological advancements, these blow molding machines also prioritize sustainability. With growing global concern over environmental issues, such as plastic waste and carbon emissions, manufacturers are under increasing pressure to adopt sustainable practices. The new machines offer energy-efficient solutions, reducing electricity consumption and minimizing their carbon footprint. This not only benefits the environment but also helps manufacturers align with evolving regulations and consumer preferences.Furthermore, the affordability of these blow molding machines presents a significant advantage for small and medium-sized enterprises (SMEs). Historically, the high cost of machinery has posed a barrier for smaller businesses wanting to enter the blow molding industry. However, with the availability of more affordable options without compromising on quality, SMEs can now compete on a level playing field, opening up new opportunities and driving economic growth.The company's commitment to customer satisfaction extends beyond product affordability. Recognizing the importance of aftersales support, the company offers comprehensive technical assistance, training programs, and readily available spare parts. This ensures that manufacturers can maximize the longevity and performance of their blow molding machines, ultimately reducing maintenance costs and minimizing downtime.As the demand for plastic products continues to rise, driven by global population growth and changing consumer habits, the blow molding industry is poised for further expansion. The introduction of affordable and innovative blow molding machines by this industry leader reflects its commitment to driving this growth by empowering manufacturers with efficient tools at a competitive price point.In conclusion, with a focus on affordability, innovation, and sustainability, the recent unveiling of a new line of blow molding machines by a global industry leader has the potential to transform the manufacturing industry. By offering efficient and versatile solutions, these machines enable businesses to increase production rates, reduce costs, and meet market demands without compromising on quality. As a result, small and medium-sized manufacturers can unlock new opportunities, contributing to economic growth and competitiveness in the blow molding industry.
High-Quality 2-4 Cavity Pet Blow Mold Machine Now Available in Canada
Title: Canadian Company Unveils Advanced 2-4 Cavity Pet Blow Mold MachineIntroduction:In a significant stride towards technological innovation, a renowned Canadian manufacturer, having established a strong presence in the field of industrial machinery, has launched an advanced 2-4 cavity PET blow mold machine. With the aim of revolutionizing the packaging industry, this cutting-edge equipment promises to increase efficiency and productivity while minimizing energy consumption and maintenance requirements. By combining the latest technological advancements with their extensive expertise, this Canadian company is set to reshape the landscape of blow molding machinery.Innovation at its Finest:The newly unveiled 2-4 cavity PET blow mold machine comes as a result of extensive research and development efforts by the talented engineers at the Canadian company. With a focus on delivering state-of-the-art solutions, this machine is equipped with advanced features that ensure superior performance and exceptional output quality.Improved Efficiency and Productivity:One of the key highlights of this PET blow mold machine is its ability to enhance efficiency and productivity levels for manufacturers. By utilizing an innovative preform heating system, this equipment achieves faster heating rates and optimized energy consumption. This translates into reduced cycle times, enabling higher production volumes without compromising the overall quality of the output.Additionally, the machine's precise control of mold closing and opening reduces the time required for mold changes, resulting in improved overall productivity. The 2-4 cavity configuration further enables simultaneous production runs, maximizing output rates and time efficiencies for manufacturers.Energy-Saving and Cost-Effective:In line with the growing emphasis on sustainability and environmentally friendly practices, the Canadian company has integrated several energy-saving features into their PET blow mold machine. By employing advanced technologies such as infrared ceramic heaters and efficient cooling systems, this equipment significantly reduces energy consumption, leading to substantial cost savings for manufacturers.Moreover, the machine's low maintenance requirements and high durability ensure a cost-effective approach for businesses. The use of high-quality components and the implementation of advanced engineering techniques guarantee a longer lifespan, minimizing the need for frequent maintenance or replacements.Quality Assurance and Flexibility:Recognizing the importance of maintaining impeccable product quality, the Canadian company has incorporated several features aimed at ensuring the highest standards.The 2-4 cavity PET blow mold machine is equipped with automatic temperature control and advanced servo-driven components that enable precise control over the blowing process. This guarantees consistent bottle integrity, uniform wall thickness, and accurate neck finishes, allowing manufacturers to deliver products of superior quality.Furthermore, the machine's flexibility allows for the production of a wide range of bottle sizes, shapes, and designs. From small containers to larger packaging solutions, this equipment accommodates diverse requirements, catering to the ever-evolving needs of packaging manufacturers.Market Impact and Future Prospects:The launch of the 2-4 cavity PET blow mold machine by the Canadian company is expected to have a significant impact on the packaging industry. Manufacturers will benefit from enhanced productivity, cost savings, and improved product quality, giving them a competitive edge in the market.Looking ahead, the Canadian company plans to amplify its research and development efforts, aiming to continuously refine and expand its range of blow molding machinery. By staying at the forefront of technological advancements, the company aims to solidify its position as a global leader in providing innovative and sustainable packaging solutions.Conclusion:With the introduction of their state-of-the-art 2-4 cavity PET blow mold machine, the Canadian company has taken a major step towards revolutionizing the packaging industry. This advanced equipment promises enhanced efficiency, increased productivity, cost savings, and superior product quality. By leveraging cutting-edge technology and their expertise, this company is paving the way for a more sustainable and innovative future in the field of packaging manufacturing.
Innovative Blow Molding Machine Offers Revolutionary Technology in Manufacturing
Apollo Blow Molding Machine, a leading manufacturer in the blow molding industry, has been making waves with its innovative technology and commitment to providing high-quality products for its customers. With a focus on delivering efficient and reliable solutions for a wide range of blow molding applications, the company has established itself as a trusted partner for businesses around the world.The Apollo Blow Molding Machine is known for its precision engineering and advanced features, which allow for seamless production processes and superior product quality. From creating custom molds to delivering fully integrated blow molding systems, Apollo offers a comprehensive range of services to meet the diverse needs of its customers.One of the key strengths of Apollo Blow Molding Machine is its ability to tailor its products and services to the specific requirements of each client. The company takes pride in its collaborative approach to working with customers, ensuring that they receive the most effective solutions for their blow molding needs. Whether it's designing a new production line or optimizing an existing system, Apollo's team of experts is dedicated to delivering results that exceed expectations.In addition to its commitment to meeting customer needs, Apollo Blow Molding Machine also prioritizes sustainability and environmental responsibility in its operations. The company continuously seeks to develop new technologies and processes that minimize waste and energy consumption, contributing to a greener, more sustainable future for the industry as a whole.With a global presence and a strong reputation for quality and reliability, Apollo Blow Molding Machine has earned the trust of numerous clients across a wide range of industries. Whether it's manufacturing packaging for consumer goods, automotive components, or industrial containers, Apollo's solutions have proven to be a valuable asset for businesses seeking to optimize their production processes.Moreover, Apollo Blow Molding Machine's dedication to continuous innovation and improvement has kept the company at the forefront of the industry. By investing in research and development, as well as staying ahead of the latest technological advancements, Apollo ensures that its products and services remain competitive and relevant in a rapidly evolving market.The success of Apollo Blow Molding Machine can be attributed not only to its cutting-edge technology and customer-centric approach, but also to the dedication and expertise of its team. The company's employees are highly skilled and experienced professionals who are passionate about delivering exceptional results for their clients. Their commitment to excellence and their ability to adapt to the ever-changing demands of the industry have been instrumental in driving Apollo's success.Looking to the future, Apollo Blow Molding Machine remains committed to upholding its values of quality, innovation, and customer satisfaction. The company is poised to continue its growth and expand its reach, while staying true to its core principles. With a solid foundation built on expertise, integrity, and forward thinking, Apollo is well positioned to lead the way in the blow molding industry for years to come.In conclusion, Apollo Blow Molding Machine has established itself as a leader in the industry, with a strong reputation for delivering exceptional products and services. Through its focus on customer collaboration, sustainability, innovation, and a talented team, the company has solidified its position as a trusted partner for businesses around the world. As it continues to grow and evolve, Apollo's commitment to excellence and its dedication to meeting the needs of its clients will undoubtedly drive its ongoing success.
New Mould Designs for Bubble Caps
Bubble Cap Mould: An Essential Tool for the Chemical IndustryBubble cap moulds are essential for the chemical industry. They are used to manufacture a wide range of products that are ubiquitous in our daily lives. From household cleaners to plastics, bubble cap moulds are used to make the caps that seal these products.Bubble cap moulds are the cornerstone of many industries and are manufactured by only a few companies worldwide. One such company that produces bubble cap moulds is headquartered in China. This company specializes in the design and manufacture of various types of moulds and has been in the industry for over 20 years.Bubble cap moulds are typically made of high-quality stainless steel. The process begins by designing the mould, which takes into account factors such as the dimensions and shape of the cap, as well as other specifications such as the material of the cap and the temperature and pressure conditions under which it will be produced.The design is then manufactured using CNC machines with high precision to ensure that the mould conforms to the exact specifications. Once the mould is completed, it is subjected to rigorous testing to ensure that it is of the highest quality standard.The chemical industry relies heavily on bubble cap moulds to produce a variety of products. Chemical companies use bubble caps to produce a variety of products, including various chemicals, household cleaners, and plastics, among others. Bubble caps are also used in the production of medical equipment, ensuring that the products are sterile and free from contamination.Bubble cap moulds are highly versatile and can be customized to fit the specific needs of each industry. They can be designed to work under varying pressure and temperature conditions and can be adapted to produce different types of caps, including twist-off and snap-on caps.One of the biggest advantages of using bubble cap moulds is their high precision. Bubble cap moulds are designed to produce caps at a high precision level, ensuring that the caps meet strict quality control standards. This level of precision also ensures that the caps are consistent in size, shape, and quality, which is important in maintaining product integrity.Moreover, bubble cap moulds are highly efficient. The moulds are designed to produce multiple caps at once, which saves a significant amount of time. This efficiency is particularly important in the chemical industry, where large volumes of products need to be produced quickly and efficiently.The Chinese company offers a wide range of bubble cap moulds to meet the needs of various industries. They specialize in producing high-quality bubble cap moulds that meet the strictest quality standards. The company has a team of highly skilled engineers and technicians who are equipped with state-of-the-art equipment to ensure the best quality products.In addition to the production of bubble cap moulds, the company offers a comprehensive range of services, including design and development, customization, repair, and maintenance. The team is available to provide technical support and advice to clients, ensuring that they get the best products and services.In conclusion, bubble cap moulds are an essential tool in the chemical industry. They are used to manufacture a wide range of products, including various chemicals, household cleaners, and plastics, among others. The Chinese company specializes in the production of high-quality bubble cap moulds that are designed to meet the strictest quality standards. With over 20 years of experience in the industry, the company offers a wide range of services, including design and development, customization, repair, and maintenance. Their team of highly skilled engineers and technicians ensures the best quality products and services, making them a valuable resource for clients in the chemical industry.
Latest Technology in Blow Moulding Machines Enhance Productivity and Efficiency
Pet Blow Moulding Machine Enhances Production Quality and CapacityWith the continuous growth of the packaging industry, the demand for high-quality and durable plastic containers in different sizes and shapes has been increasing rapidly. In response to this, many manufacturers have invested in new technologies and equipment to increase production efficiency and quality standards. One such technology that has revolutionized the packaging industry is the Pet Blow Moulding Machine.Pet Blow Moulding Machine is a cutting-edge technology that is used to manufacture plastic containers of different shapes and sizes. This machine works by heating and stretching a preform (a tube of plastic) until it reaches the desired shape and size. The three main types of Pet Blow Moulding Machines are the Injection Stretch Blow Moulding Machine (ISBM), Extrusion Blow Moulding Machine (EBM), and Injection Blow Moulding Machine (IBM). Each type has its own unique features and benefits depending on the production requirements.The Pet Blow Moulding Machine has become a preferred choice for manufacturers in the packaging industry because it offers several advantages over other traditional manufacturing methods. Firstly, this technology is easy to operate and maintain, requiring minimal supervision and less downtime. This makes it possible for manufacturers to produce plastic containers in large quantities within a short time, meeting the increasing demand for their products.Secondly, the Pet Blow Moulding Machine produces high-quality containers with uniform thickness and consistent shapes. The machines are equipped with advanced automation systems that monitor, control and track the production process, ensuring consistent and reliable output. This has significantly reduced the rejection rate of defective plastic containers, saving manufacturers time and resources that would otherwise be wasted in sorting out sub-standard products.Thirdly, the Pet Blow Moulding Machine is highly flexible and can produce plastic containers of various shapes, sizes, and colors. This makes it possible for manufacturers to customize their designs to meet the specific needs of their customers, making them stand out in a highly competitive market. With the Pet Blow Moulding Machine, manufacturers can produce containers for different applications such as food and beverages, cosmetics, pharmaceuticals, and household goods.One company that has leveraged the benefits of the Pet Blow Moulding Machine to enhance its production quality and capacity is X company. This company is a leading manufacturer of plastic containers in the Philippines, specializing in the production of PET bottles, jars, and containers for various industries. They have invested in the latest Pet Blow Moulding Machines, including the ISBM, IBM, and EBM, to increase their production efficiency and quality standards.According to the company's spokesperson, "Our investment in the Pet Blow Moulding Machine has significantly improved our production capacity and quality standards. We can produce high-quality plastic containers in large quantities within a short time, reducing lead times and meeting the increasing demand for our products. The machines are easy to operate and maintain, and we have experienced less downtime since we acquired them."The spokesperson further added, "Our Pet Blow Moulding Machines produce consistent and uniform containers with a high level of accuracy, meeting the strict quality standards of our clients. We can also produce plastic containers of various sizes, shapes, and colors, which has enabled us to expand our product range and explore new market opportunities."In conclusion, the Pet Blow Moulding Machine has revolutionized the packaging industry by offering manufacturers an easy-to-use, high-quality, and reliable manufacturing method. This technology has enhanced production capacity, reduced rejection rates, and increased flexibility for manufacturers, making it a preferred choice for the production of plastic containers. The investment by X Company in these machines demonstrates the value of this technology in the packaging industry and how it can drive business growth and success.
High-Quality Injection Molding for Small Parts: A Guide
Injection Molding Small Parts: A Specialty of {Company Name}{Company Name} is a leading manufacturer of injection molded small parts for a wide range of industries. With a commitment to providing high-quality, precision parts, {Company Name} has become a trusted partner for companies all over the world.Injection molding is a manufacturing process in which molten material is injected into a mold, where it cools and solidifies to form the desired shape. This process allows for the production of complex and detailed parts with a high level of consistency and accuracy.{Company Name} specializes in the production of small parts, ranging from tiny components for electronic devices to intricate parts for medical equipment. The company has invested in state-of-the-art injection molding equipment and technology, allowing them to produce parts with tight tolerances and intricate geometries.{Company Name} works closely with their clients to understand their unique needs and requirements. Whether it's developing a new product or improving an existing one, {Company Name} is dedicated to delivering the highest quality parts that meet the specific demands of each project.The team at {Company Name} is comprised of skilled engineers and technicians who have extensive experience in injection molding. They are able to provide valuable insights and recommendations to help clients optimize their designs for injection molding, leading to cost savings and improved efficiency.One of the key advantages of injection molding is its ability to produce large volumes of parts with minimal waste. This makes it a cost-effective manufacturing process for small parts, as it allows for high production rates and consistent quality.In addition to their expertise in injection molding, {Company Name} also offers secondary services such as assembly, packaging, and quality inspection. This allows them to provide a complete solution for their clients, streamlining the production process and ensuring that the final product meets the highest standards.{Company Name} is dedicated to maintaining the highest standards of quality and consistency in their production processes. They have implemented rigorous quality control measures to ensure that every part meets the specified requirements and standards.With a focus on innovation and continuous improvement, {Company Name} is constantly exploring new technologies and materials to enhance their injection molding capabilities. This allows them to stay at the forefront of the industry and provide their clients with the most advanced solutions.The company's dedication to quality and customer satisfaction has earned them a solid reputation in the industry. They have built long-lasting relationships with clients in a wide range of industries, including automotive, electronics, medical, and consumer goods.{Company Name} is proud to be a trusted partner for companies around the world, providing them with high-quality injection molded small parts that meet their specific needs. With a commitment to innovation, quality, and customer satisfaction, the company continues to be a leader in the injection molding industry.In conclusion, {Company Name} is a leading manufacturer of injection molded small parts, offering a wide range of capabilities and services to meet the unique needs of their clients. With a focus on quality, innovation, and customer satisfaction, {Company Name} is dedicated to delivering the highest quality parts for a wide range of industries.
Explore the Latest Innovation in Pet Blow Molders for Efficient Plastic Bottle Production
Title: Innovative Pet Blow Molders Revolutionize Plastic Bottle ProductionIntroduction:In today's dynamic consumer market, the demand for sustainable packaging solutions is rapidly increasing. To address this growing need, several companies are employing innovative techniques to manufacture environmentally friendly plastic bottles. One such pioneering entity is {Company Name}. Recognized for their groundbreaking Pet Blow Molders, {Company Name} is transforming the plastic bottle production industry by introducing cutting-edge technology that improves efficiency, reduces waste, and enhances sustainability.1. Enhanced Efficiency:With the goal of meeting the rising demand for plastic bottles without compromising on quality, {Company Name} has developed state-of-the-art Pet Blow Molders. These machines utilize advanced automation technology to optimize production processes, resulting in boosted efficiency and reduced production time. By streamlining operations, {Company Name} empowers businesses to meet consumer demands promptly, facilitating the growth of the plastic packaging industry.2. Focus on Sustainability:In response to the mounting concern about plastic waste, {Company Name} has integrated sustainability measures into their Pet Blow Molders. By using PET (polyethylene terephthalate) material, a widely recyclable plastic, these machines allow for the production of bottles that can be repurposed and recycled. This ecological approach aligns with global efforts to foster a circular economy, reducing the environmental impact of plastic packaging.3. Cutting-edge Technology:A major strength of {Company Name} lies in their commitment to innovation. Their Pet Blow Molders are engineered with cutting-edge technology that ensures maximum precision and durability. These machines are capable of creating bottles in various shapes and sizes, catering to the unique requirements of different industries. Equipped with next-generation features, {Company Name}'s Pet Blow Molders are quickly becoming the go-to choice for businesses seeking top-quality plastic bottles.4. Versatile Applications:{Company Name}'s Pet Blow Molders are incredibly versatile, accommodating a wide range of industry needs. Whether it is the food and beverage sector, household products, cosmetics, or pharmaceuticals, these machines are capable of producing bottles that meet the highest quality standards across diverse industries. The adaptability of these Pet Blow Molders positions {Company Name} as a reliable partner for businesses seeking innovative packaging solutions.5. Unparalleled Customer Support:Understanding the importance of comprehensive customer support, {Company Name} offers comprehensive technical assistance to ensure optimal performance of their Pet Blow Molders. Their skilled team of professionals provides swift and efficient maintenance services, minimizing downtime and maximizing productivity. This unparalleled commitment to customer satisfaction has earned {Company Name} a reputation for reliability and trustworthiness within the industry.Closing:In conclusion, {Company Name} is revolutionizing the plastic bottle production industry with their innovative Pet Blow Molders. By combining enhanced efficiency, sustainability, cutting-edge technology, versatility, and unparalleled customer support, {Company Name} is setting new benchmarks for contemporary plastic packaging solutions. Embracing these groundbreaking machines will not only enable businesses to meet increasing consumer demands but also contribute towards a greener and more sustainable future.
New Injection Mold Technology for Pet Preform Production
Yizumi Injection Mold Unveils State-of-the-Art Solution for PET Preform ManufacturingIn recent years, the demand for PET preforms has soared, and the market for these essential components shows no sign of slowing down. To cater to this increasing demand, Yizumi Injection Mold has unveiled its revolutionary injection mold solution, designed to revolutionize the PET preform manufacturing industry.With a history of excellence spanning several years, Yizumi Injection Mold has established itself as a leader in the injection molding industry. The company's commitment to continuously innovate and improve its technologies has resulted in the introduction of this game-changing mold solution.The newly unveiled mold by Yizumi Injection Mold is engineered to meet the ever-growing demands of the PET preform market, offering superior efficiency, precision, and reliability. By leveraging cutting-edge manufacturing techniques and state-of-the-art materials, the mold ensures optimal performance and consistency, streamlining the PET preform manufacturing process.Key to the mold's success is the integration of advanced technologies that enhance its functionality and durability. Yizumi Injection Mold's engineers have employed meticulous precision engineering and rigorous testing to deliver exceptional results. The mold boasts superior cooling efficiency, ensuring faster production cycles and minimized downtime.Furthermore, the mold has been designed with a focus on longevity and durability. It is built to withstand the rugged demands of high-volume production, providing manufacturers with a reliable and long-lasting solution that maximizes their return on investment.In addition to its impressive technical specifications, the Yizumi Injection Mold for PET preforms offers unmatched versatility. The mold is compatible with a wide range of PET resins, allowing manufacturers to adapt to varying market requirements swiftly. This flexibility not only provides cost-saving benefits but also opens up new avenues for product innovation and diversification.The company's commitment to sustainability shines through in the Yizumi Injection Mold design. The mold incorporates eco-friendly features that reduce energy consumption and minimize waste generation. By optimizing the cooling process and incorporating efficient material distribution channels, the mold ensures minimal environmental impact without compromising on performance.Yizumi Injection Mold's commitment to customer satisfaction is evident in its comprehensive after-sales service. The company offers extensive technical support, assisting manufacturers in optimizing their production processes, troubleshooting issues, and ensuring continuous productivity. Additionally, the prompt availability of spare parts and professional maintenance services ensures minimal downtime, maximizing manufacturing efficiency.With the launch of this groundbreaking mold, Yizumi Injection Mold solidifies its position as an industry innovator. By combining cutting-edge technology, reliability, and exceptional versatility, the company offers a comprehensive solution for PET preform manufacturers worldwide.As the demand for PET preforms continues to rise, Yizumi Injection Mold remains at the forefront of the industry, constantly striving to improve and exceed customer expectations. With their innovative mold solution, they provide manufacturers with the tools they need to stay competitive in a dynamic market.In summary, Yizumi Injection Mold's newly unveiled solution for PET preform manufacturing sets a new standard in the industry. With its advanced technology, reliability, and environmental consciousness, the mold offers manufacturers unrivaled efficiency, flexibility, and sustainability. Yizumi Injection Mold's commitment to customer satisfaction, backed by comprehensive after-sales services, further strengthens the company's position as a global leader in the injection molding industry.
Ultimate Guide to Choosing the Best Cosmetic Packaging for Your Products
Cosmetic Packaging: A Look at the Latest Trends and Innovations in Beauty PackagingIn recent years, the beauty industry has experienced a significant shift towards more sustainable and eco-friendly practices. This has extended to the packaging of cosmetic products, with brands and manufacturers increasingly seeking out sustainable and innovative packaging solutions. With this in mind, {Company Name} has been at the forefront of developing cutting-edge cosmetic packaging that not only meets the needs of their clients but also aligns with their commitment to sustainability.{Company Name} has a long-standing reputation for producing high-quality cosmetic packaging for some of the leading beauty brands in the industry. With a focus on innovation and sustainability, the company has been able to stay ahead of the curve in a rapidly evolving market. Their team of experts is constantly researching and designing new packaging solutions that not only meet the functional requirements of their clients but also reflect the latest trends and consumer preferences.One of the key trends in cosmetic packaging is the move towards more sustainable and eco-friendly materials. {Company Name} has been actively developing and promoting the use of materials such as recycled plastics, biodegradable plastics, and glass, all of which have a lower impact on the environment. In addition to using sustainable materials, the company also focuses on designing packaging with minimal environmental impact, such as reducing the use of unnecessary packaging and incorporating innovative designs that minimize waste.In line with the growing demand for sustainable packaging, {Company Name} has also been exploring new technologies and processes to further improve the environmental performance of their products. This includes investing in new manufacturing techniques that reduce energy consumption and waste, as well as exploring the potential of alternative materials and bioplastics. By integrating these sustainable practices into their operations, the company is not only meeting the demands of their clients but also contributing to the overall sustainability of the beauty industry.Another key trend in cosmetic packaging is the emphasis on functionality and user experience. {Company Name} recognizes the importance of creating packaging that not only looks aesthetically pleasing but also enhances the overall experience of using the product. This includes designing packaging with convenient dispensing systems, ergonomic shapes, and easy-to-use features that make the product more appealing to consumers.In addition to functionality, {Company Name} has also been incorporating innovative designs and packaging concepts that appeal to the modern consumer. This includes the use of bold colors, striking graphics, and unique shapes that stand out on the shelves and attract the attention of the target audience. By staying ahead of the curve in terms of design and aesthetics, the company is able to offer their clients packaging solutions that are both visually appealing and on-trend with the latest consumer preferences.As the beauty industry continues to evolve, {Company Name} remains committed to staying at the forefront of cosmetic packaging innovation. By focusing on sustainability, functionality, and design, the company is able to offer their clients cutting-edge packaging solutions that meet the demands of the modern consumer. With a strong emphasis on research and development, {Company Name} is well-positioned to continue driving innovation in the cosmetic packaging industry for years to come.
The Importance of Auxiliary Equipment in Blow Molding
Title: Essential Auxiliary Equipment in Blow Molding IndustryIntroduction:Blow molding is a widely used manufacturing process in the production of plastic containers and bottles. To ensure the efficiency and quality of the blow molding process, the utilization of various auxiliary equipment is of paramount importance. These tools aid in enhancing productivity, maintaining consistent output, and ensuring the overall success of the blow molding operation. In this article, we will explore the significance of auxiliary equipment in the blow molding industry, encompassing its role, types, and benefits.Role of Auxiliary Equipment:Auxiliary equipment plays a pivotal role in supporting and enhancing the efficiency of the blow molding process. These devices are designed to assist in different stages of the manufacturing cycle, such as material handling, controlling temperature, cutting, trimming, and a myriad of other operations. By integrating auxiliary equipment, manufacturers can streamline their production lines, reduce manual labor, enhance product quality, and achieve higher levels of output.Types of Auxiliary Equipment in Blow Molding:1. Material Handling Equipment: - Conveyors: These devices assist in moving raw materials, preforms, and finished products through each stage of the blow molding process, ensuring smooth material flow and minimizing human intervention. - Hoppers: Hoppers aid in the organized storage and feeding of plastic resins or pellets into the extruder. They help regulate the supply of raw materials, preventing interruptions and ensuring an uninterrupted production line.2. Temperature Control Equipment: - Chillers: These devices are crucial for maintaining consistent cooling temperatures during the blow molding process. Chillers control the temperature of molds, ensuring the final product's dimensional accuracy and quality. - Mold Temperature Controllers: These controllers regulate the temperature of the molds themselves, preventing fluctuation and ensuring consistent heat distribution. By maintaining optimal mold temperatures, manufacturers can achieve faster production cycles and improve product quality.3. Cutting and Trimming Equipment: - Guillotine Cutters: These devices aid in cutting or trimming the excess material from the finished blow-molded items. They enable precise and accurate trimming, contributing to a polished final product. - Deflashing Equipment: Deflashing machines are used to remove excess material or flash from the finished products. These machines improve the overall appearance and functionality of the final blow-molded items.4. Quality Control Equipment: - Inspection Systems: These systems employ advanced imaging technologies to detect and eliminate any defects or inconsistencies in the finished products. By incorporating inspection systems, manufacturers can maintain the desired quality levels and ensure consumer satisfaction.Benefits of Incorporating Auxiliary Equipment:1. Improved Efficiency: Auxiliary equipment streamlines the manufacturing process, reducing manual labor and improving overall efficiency. It decreases downtime and minimizes errors, resulting in higher productivity and increased profitability.2. Enhanced Product Quality: By incorporating auxiliary equipment, manufacturers can achieve consistent product quality. Temperature control equipment, cutting and trimming devices, and inspection systems all contribute to delivering flawless products to the market.3. Cost Reduction: The integration of auxiliary equipment reduces material wastage, improves energy efficiency, and minimizes the need for manual labor. These factors lead to significant cost savings for manufacturers in the long run.4. Scalability: Auxiliary equipment is crucial for accommodating increased production volumes. By having the appropriate tools in place, manufacturers can easily scale their operations without compromising on quality or efficiency.Conclusion:Auxiliary equipment is indispensable in the blow molding industry, enabling manufacturers to achieve efficient and high-quality production processes. The integration of material handling equipment, temperature control devices, cutting and trimming tools, and quality control systems ensures smooth operations, consistent output, and reduced costs. By leveraging the benefits of auxiliary equipment, manufacturers can stay competitive in the ever-evolving market of blow molding.
Blow Molding Machines: An In-Depth Look at Pricing and Factors to Consider
Blow Molding Machine Price: Driving Innovation and Affordability in the Manufacturing IndustryThe blow molding industry has experienced significant growth in recent years, fueled by increasing demand for plastic packaging and a rise in consumer preferences for affordable and lightweight materials. As a result, companies are constantly seeking innovative solutions to improve production efficiency and lower costs.One prominent player in this field, a global leader in blow molding machinery, has recently unveiled a new line of blow molding machines that promise to revolutionize the manufacturing industry. With a focus on affordability without compromising quality, the company aims to equip manufacturing businesses with highly efficient tools that meet their production needs at a competitive price point.Blow molding machines are essentially used to create hollow plastic parts and containers in a wide range of industries, including food and beverage, cosmetics, pharmaceuticals, and automotive. These machines employ a process of melting plastic resins and stretching them into a desired shape, resulting in strong and lightweight products.The newly introduced blow molding machines by this industry-leading company incorporate advanced technology and numerous features designed to enhance productivity and reduce downtime. These machines offer improved automation, precision controls, and faster cycle times, ensuring more efficient production rates. By streamlining the manufacturing process, businesses can achieve higher output and lower costs, ultimately resulting in a competitive edge.One of the standout features of this new line of blow molding machines is their versatility. With the ability to produce a wide variety of shapes and sizes, these machines cater to the diverse needs of manufacturers. Whether it's producing bottles, containers, or other bespoke plastic products, the flexibility of these machines allows businesses to adapt to changing market demands without significant retooling or investment.In addition to their technological advancements, these blow molding machines also prioritize sustainability. With growing global concern over environmental issues, such as plastic waste and carbon emissions, manufacturers are under increasing pressure to adopt sustainable practices. The new machines offer energy-efficient solutions, reducing electricity consumption and minimizing their carbon footprint. This not only benefits the environment but also helps manufacturers align with evolving regulations and consumer preferences.Furthermore, the affordability of these blow molding machines presents a significant advantage for small and medium-sized enterprises (SMEs). Historically, the high cost of machinery has posed a barrier for smaller businesses wanting to enter the blow molding industry. However, with the availability of more affordable options without compromising on quality, SMEs can now compete on a level playing field, opening up new opportunities and driving economic growth.The company's commitment to customer satisfaction extends beyond product affordability. Recognizing the importance of aftersales support, the company offers comprehensive technical assistance, training programs, and readily available spare parts. This ensures that manufacturers can maximize the longevity and performance of their blow molding machines, ultimately reducing maintenance costs and minimizing downtime.As the demand for plastic products continues to rise, driven by global population growth and changing consumer habits, the blow molding industry is poised for further expansion. The introduction of affordable and innovative blow molding machines by this industry leader reflects its commitment to driving this growth by empowering manufacturers with efficient tools at a competitive price point.In conclusion, with a focus on affordability, innovation, and sustainability, the recent unveiling of a new line of blow molding machines by a global industry leader has the potential to transform the manufacturing industry. By offering efficient and versatile solutions, these machines enable businesses to increase production rates, reduce costs, and meet market demands without compromising on quality. As a result, small and medium-sized manufacturers can unlock new opportunities, contributing to economic growth and competitiveness in the blow molding industry.
High-Quality 2-4 Cavity Pet Blow Mold Machine Now Available in Canada
Title: Canadian Company Unveils Advanced 2-4 Cavity Pet Blow Mold MachineIntroduction:In a significant stride towards technological innovation, a renowned Canadian manufacturer, having established a strong presence in the field of industrial machinery, has launched an advanced 2-4 cavity PET blow mold machine. With the aim of revolutionizing the packaging industry, this cutting-edge equipment promises to increase efficiency and productivity while minimizing energy consumption and maintenance requirements. By combining the latest technological advancements with their extensive expertise, this Canadian company is set to reshape the landscape of blow molding machinery.Innovation at its Finest:The newly unveiled 2-4 cavity PET blow mold machine comes as a result of extensive research and development efforts by the talented engineers at the Canadian company. With a focus on delivering state-of-the-art solutions, this machine is equipped with advanced features that ensure superior performance and exceptional output quality.Improved Efficiency and Productivity:One of the key highlights of this PET blow mold machine is its ability to enhance efficiency and productivity levels for manufacturers. By utilizing an innovative preform heating system, this equipment achieves faster heating rates and optimized energy consumption. This translates into reduced cycle times, enabling higher production volumes without compromising the overall quality of the output.Additionally, the machine's precise control of mold closing and opening reduces the time required for mold changes, resulting in improved overall productivity. The 2-4 cavity configuration further enables simultaneous production runs, maximizing output rates and time efficiencies for manufacturers.Energy-Saving and Cost-Effective:In line with the growing emphasis on sustainability and environmentally friendly practices, the Canadian company has integrated several energy-saving features into their PET blow mold machine. By employing advanced technologies such as infrared ceramic heaters and efficient cooling systems, this equipment significantly reduces energy consumption, leading to substantial cost savings for manufacturers.Moreover, the machine's low maintenance requirements and high durability ensure a cost-effective approach for businesses. The use of high-quality components and the implementation of advanced engineering techniques guarantee a longer lifespan, minimizing the need for frequent maintenance or replacements.Quality Assurance and Flexibility:Recognizing the importance of maintaining impeccable product quality, the Canadian company has incorporated several features aimed at ensuring the highest standards.The 2-4 cavity PET blow mold machine is equipped with automatic temperature control and advanced servo-driven components that enable precise control over the blowing process. This guarantees consistent bottle integrity, uniform wall thickness, and accurate neck finishes, allowing manufacturers to deliver products of superior quality.Furthermore, the machine's flexibility allows for the production of a wide range of bottle sizes, shapes, and designs. From small containers to larger packaging solutions, this equipment accommodates diverse requirements, catering to the ever-evolving needs of packaging manufacturers.Market Impact and Future Prospects:The launch of the 2-4 cavity PET blow mold machine by the Canadian company is expected to have a significant impact on the packaging industry. Manufacturers will benefit from enhanced productivity, cost savings, and improved product quality, giving them a competitive edge in the market.Looking ahead, the Canadian company plans to amplify its research and development efforts, aiming to continuously refine and expand its range of blow molding machinery. By staying at the forefront of technological advancements, the company aims to solidify its position as a global leader in providing innovative and sustainable packaging solutions.Conclusion:With the introduction of their state-of-the-art 2-4 cavity PET blow mold machine, the Canadian company has taken a major step towards revolutionizing the packaging industry. This advanced equipment promises enhanced efficiency, increased productivity, cost savings, and superior product quality. By leveraging cutting-edge technology and their expertise, this company is paving the way for a more sustainable and innovative future in the field of packaging manufacturing.